Nav24 Shop Floor – your solution for production data recording
Shop Floor is a modern mobile application designed for precise data recording directly from the production floor. Thanks to full integration with the Microsoft Dynamics 365 Business Central system, operating in the SaaS model, our solution ensures seamless data management and synchronization with the ERP system
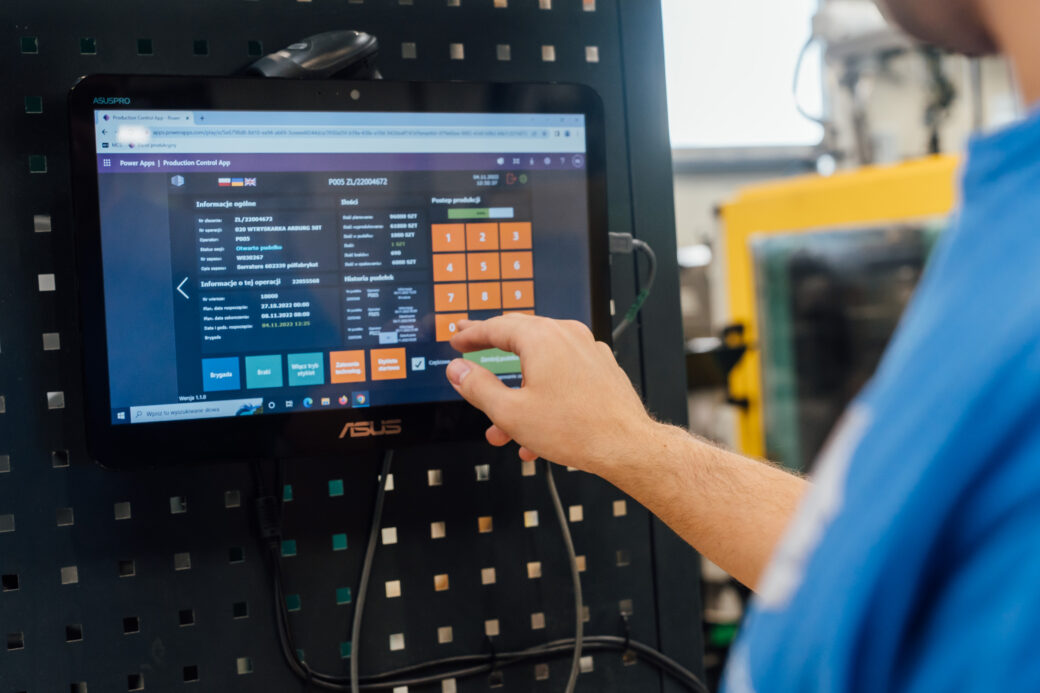
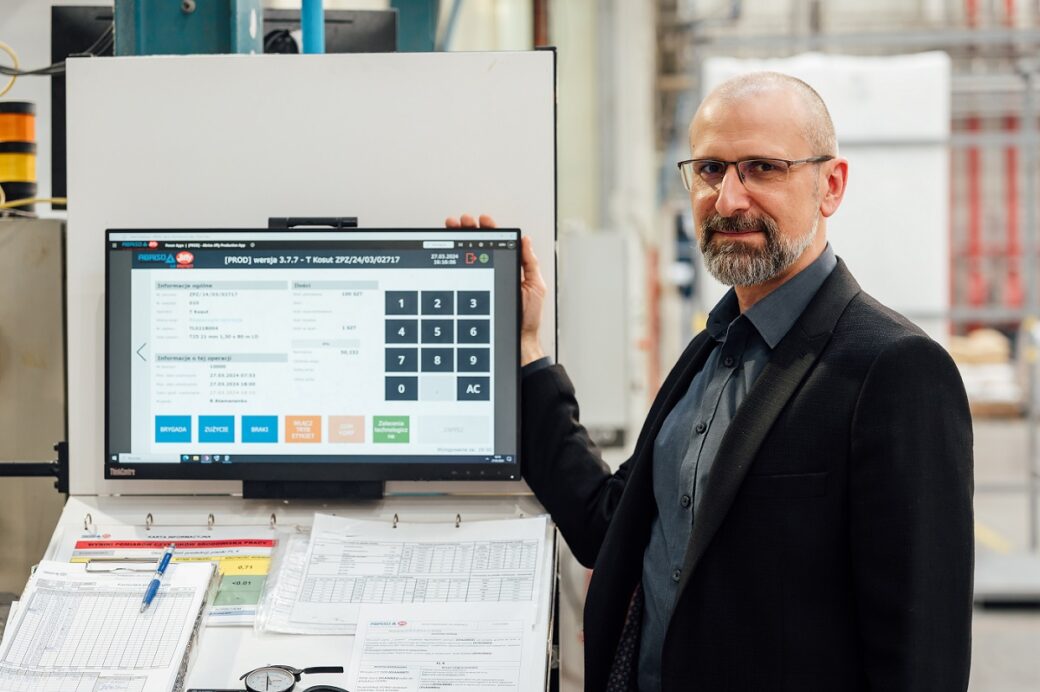
Collect data straight from production floor
The Nav24 Shop Floor application is fully customizable to the unique needs of any manufacturing company. We offer flexibility in configuration, allowing for a perfect fit of functionalities to the specific processes and requirements of your business. This enables full control and optimization of production processes, leading to increased efficiency and data accuracy.
Why is it worth it?
Quick implemenationThanks to Low Code technology and integration with Business Central, the implementation of our system is quick and does not require significant labor effort
Flexibility and scalability Our solution can be easily adapted to the specific needs of any company, regardless of the industry.
Full automation and optimization By automating key production processes, companies can save time, reduce operational costs, and avoid costly production errors.
Security and transparency Instant control over production data and digital quality control ensure full transparency of operations.
The Shop Floor is the answer to many challenges faced by manufacturing companies
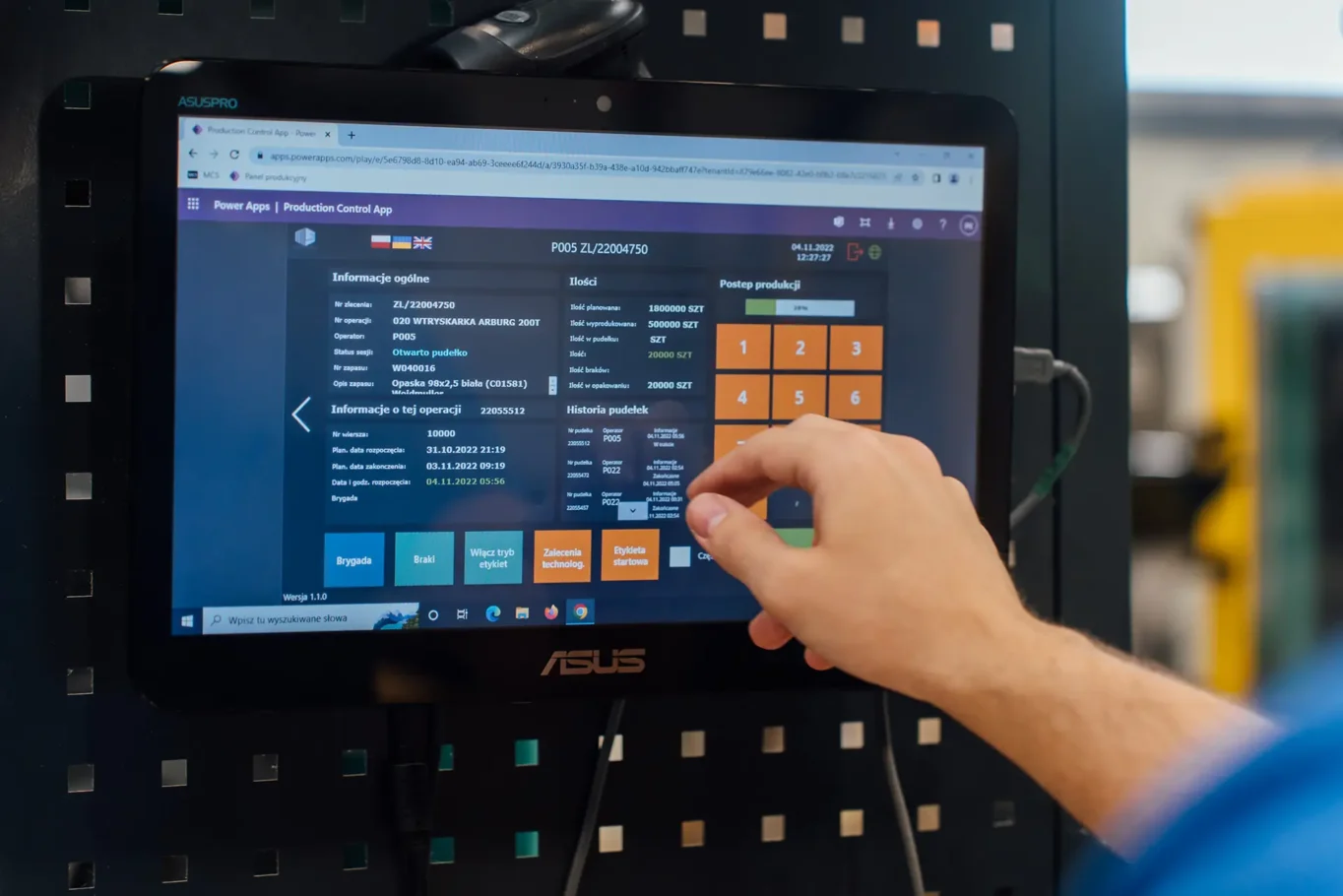
I don't know the cost of manufacturing the product, and I am not sure if the final price is appropriate.
As a result, sales are often below the profitability threshold. Recording data with job-level accuracy allows for the proper calculation of the margin.
Operators record production data on paper sheets.
The Shop Floor allows data to be recorded on mobile devices (tablets/touchscreen computers). The start-stop functionality for individual operations on specific jobs minimizes both the time required for data entry and the risk of errors.
Operators enter incorrect data, such as the wrong date or job number.
The Shop Floor utilizes automation to retrieve data from Business Central. Also, operators don't have the ability to modify predefined data directly on the panel, which speeds up the workflow and eliminates errors.
Operators forget or delay entering data regarding raw material usage.
We have introduced a functionality that checks the total amount of components used in relation to the quantity already produced. If the usage is relatively lower, notifications are displayed to operators, which helps ensure timely data entry.
Operators do not record data regarding the quantity and causes of defects
The causes of defects are retrieved from the ERP system's dictionary table, and the defects themselves are recorded on the panel by operators during the ongoing machine operation.
The need to hire additional personnel for manually entering data into the ERP system increases costs.
The Shop Floor uses automatic data replication from the app to the Business Central system, automatic data posting, validation, and a notification mechanism, which eliminates the need for hiring additional personnel for data entry.
No real-time monitoring of production status.
Our solution offers an additional application for production managers, which provides a real-time view of the current status of the production floor. The application displays all workstations and production cells, the current production orders each cell is working on, and the progress of production. This allows managers to monitor the situation on the floor continuously, enabling quick responses to any issues and optimizing production processes.
Available operating modes.
Kiosk
- The Shop Floor allows work in Kiosk Mode, where multiple operators can use a single device. The system automatically logs when a person starts working on a task, and after finishing, it automatically logs the operator out.
- Thanks to automatic logouts, the system prevents accidental errors related to assigning work to the wrong person. Kiosk mode is an ideal solution for workstations where multiple operators use the same device.
Kiosk
Continuous Operation Mode
- In continuous mode, while performing a task, the operator is not logged out, which allows for continuous, uninterrupted work at the workstation. This enables operators to efficiently carry out tasks without the need to pause for logging in or out of the system.
- Working in continuous mode increases efficiency at workstations where uninterrupted work is crucial, such as in long-lasting production processes, eliminating the need for repeated logins.
Continuous Operation Mode
Shop Floor - Selected Functionalities
Nav24 Shop Floor is available on Microsoft AppSource
See the MES system Nav24 Shop Floor Panel directly on Microsoft AppSource.
AppSource is a place where you can find Microsoft-approved extensions for application functionalities.
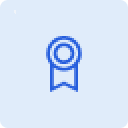
Nav24 Shop Floor
Nav24 Sp. z o.o.
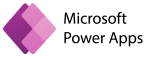
The app is used to manage most of the key processes related to the recording of production data.
Go to AppSource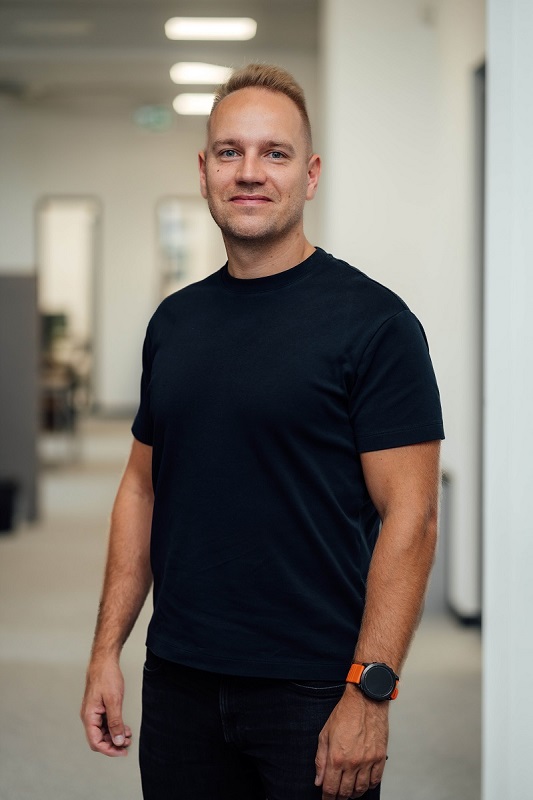