Modern IT systems can significantly enhance the efficiency of production processes. However, many companies in the industry still rely on outdated planning methods, including paper-based ones. We'll guide you on how to bring a manufacturing company into the digital world and streamline processes with modern software.
What is an ERP system for production?
Enterprise Resource Planning (ERP) tools are information systems whose primary purpose is to integrate all business processes within a company, from purchasing and production to warehousing, logistics, marketing, sales, and accounting. Simple inventory control applications supporting inventory management started emerging in the 1960s. Growing needs and technological advancements led to the development of Material Resource Planning (MRP) systems and later MRP II, designed for material requirement planning. These systems served as the foundation for the first ERP systems and their evolution, known as ERP II. Their capabilities were gradually expanded to include additional modules, allowing for production planning and financial management, among others. Today, ERP systems can manage virtually all areas of a company. In this article, we will primarily focus on production planning using the Dynamics 365 Business Central ERP system.
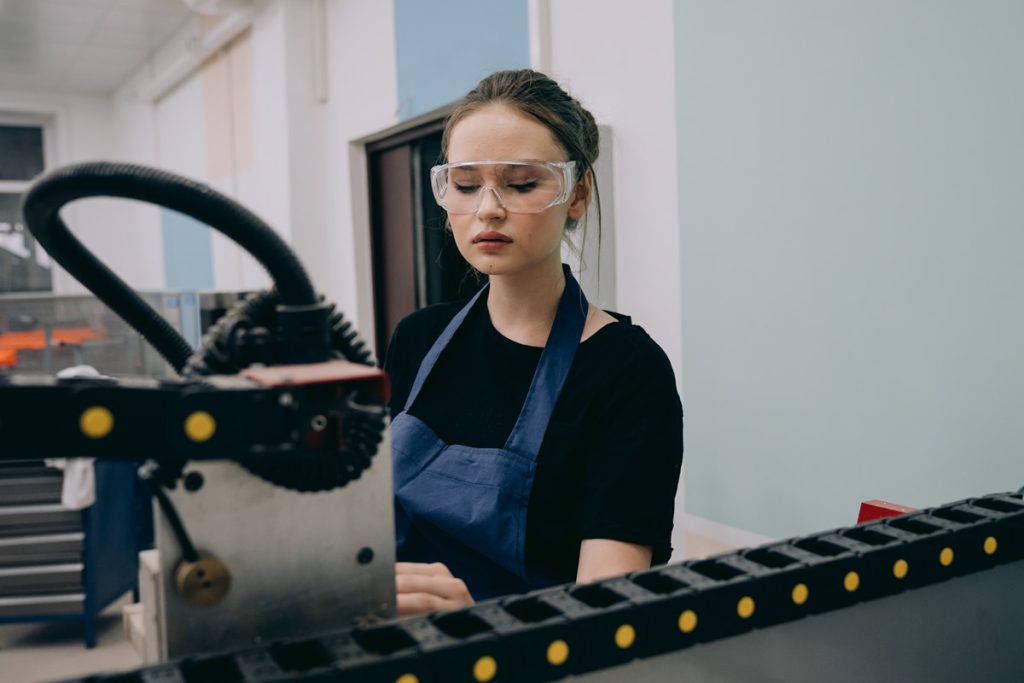
Benefits of implementing an ERP system
How many times in your company has information about a machine breakdown reached decision-makers with significant delays? Or, due to poor material demand planning, have you run out of essential materials for a production order? As a result, production faces delays or even comes to a halt. An ERP system, combined with extensions such as a Manufacturing Execution System (MES) application like our proprietary Production Panel, enables the collection of data directly from the production floor. Thanks to direct digital connectivity with machines, you receive all necessary data regarding the production process instantly. Streamlining data flow between departments also enables efficient inventory management and procurement planning. Production managers can monitor in real-time which machines are currently in use, which are idle or delayed, allowing them to take timely corrective actions. Meanwhile, the procurement department can respond to reported material requirements and potential shortages. Therefore, implementing an ERP system facilitates making the right decisions and optimizing production processes.
How does an ERP system affect inventory management in production?
What functionalities should a good ERP system have to support inventory management? First and foremost, it should allow for defining the product structure and the technological process, enabling the creation of complex production Bills of Materials (BOMs). MRP planning sheets help in planning semi-finished products, raw materials, and materials needed to fulfill the production plan.
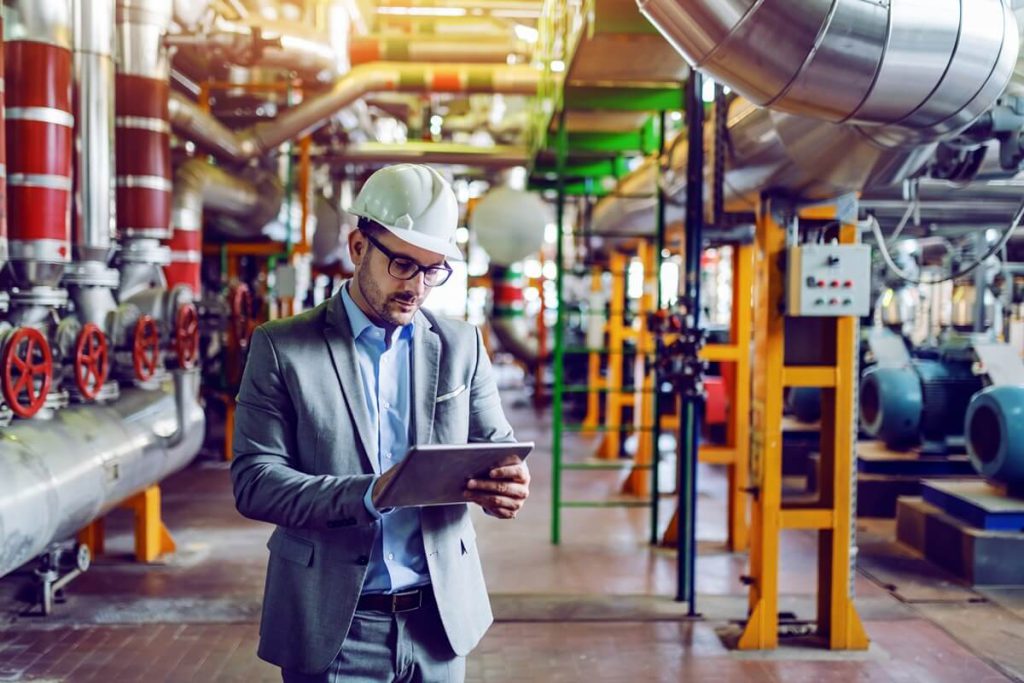
It's also essential to pay attention to the inventory card database, which serves as the central repository of information about materials, goods, semi-finished products, or finished products. All transactions that affect the decrease or increase in the stock level are immediately recorded in the inventory card. In situations where the inventory balance doesn't align with the established assumptions, you can individually define the parameters for re-planning in the inventory card.
How does an ERP system support the production planning process?
What does production planning look like in an ERP system? This process encompasses various elements, such as production BOMs, MRP planning sheets (Material Requirements Planning), operations in the technological process using workstations and work centers, as well as cost accounting. Production BOMs define the structure of products and specify which components and materials are needed for production. On the other hand, MRP planning sheets aid in inventory management and determine how much material must be available at any given time to execute the production plan.
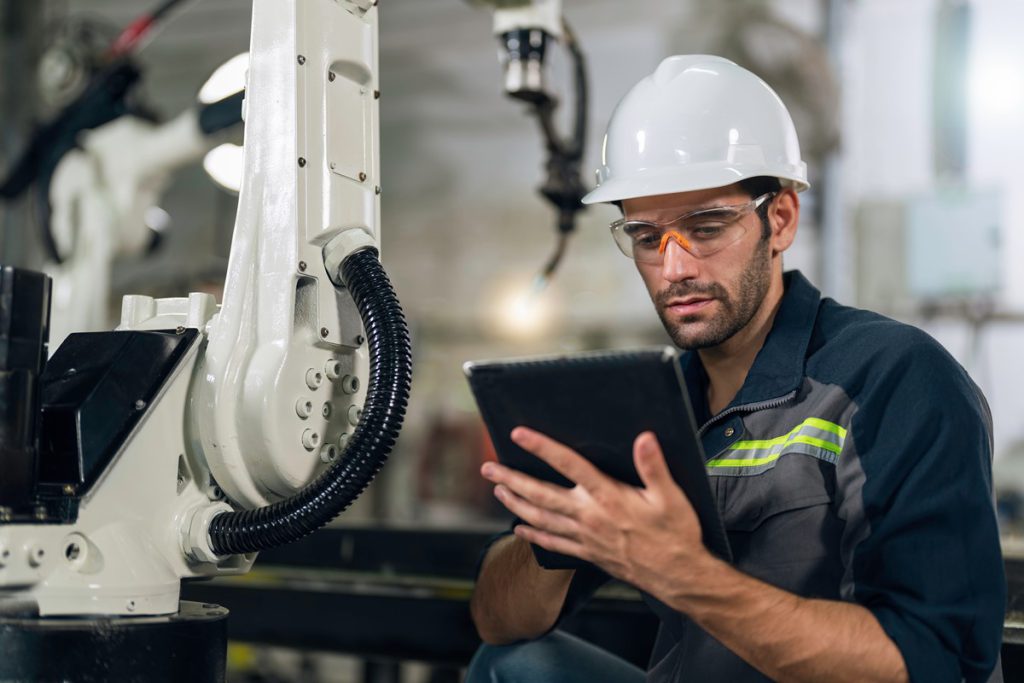
Defining operations in the technological process involves specifying the sequence of activities and the use of workstations and work centers. Setup time, unit time, and other auxiliary times are taken into account during the production planning process to estimate the time required for each operation. Cost accounting is also a crucial aspect of production planning. An ERP system can automatically track production-related costs, including materials, labor, energy, and other resources, enabling precise monitoring and control of production costs. With access to a wealth of essential information, it becomes easier to create an efficient production plan that considers the current capabilities of the production department.
Does an ERP system for production integrate with other systems in the company?
To ensure proper functionality, an ERP system must seamlessly integrate with other systems and applications used in the company. For example, the Business Central ERP system mentioned earlier, being part of the Dynamics 365 family, naturally collaborates with all Microsoft products. Integrating Business Central with Microsoft 365 suite solutions or CRM Dynamics 365 Sales streamlines cooperation between different company departments and expedites order fulfillment processes. Business Central can also integrate with applications developed using Power Apps or third-party solutions, such as optical character recognition programs.
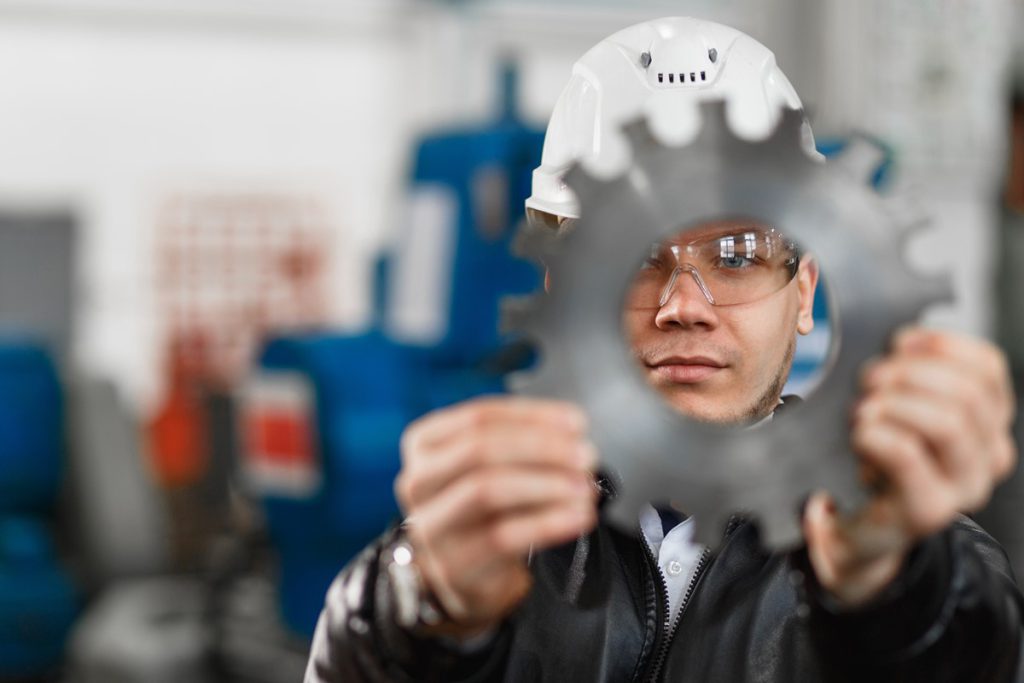
What are the implementation possibilities for an ERP system for production?
When opting for the ERP system Business Central, there are two implementation options. The first is called a rapid implementation. It is designed for small and medium-sized companies that either do not have an ERP solution or have existing tools that do not meet all their requirements. Launching a ready-made package tailored specifically to the needs of manufacturing companies allows for quick system deployment and familiarity with its capabilities. Thanks to Business Central's flexibility, you can adapt it to your company's individual needs after implementation. The second option is a personalized implementation. Before deploying the ERP system, modifications are prepared based on the specific requirements of customers. This type of implementation takes longer, but the system is perfectly tailored to the company's individual requirements from the outset.
For more information on the capabilities offered by ERP systems in manufacturing companies and various implementation options, please visit the dedicated manufacturing industry page. We also encourage you to explore other blog articles dedicated to solutions for manufacturing companies.