You want to sell several products to your customer. You create a sales document, fill in the lines with inventory, and enter the quantities requested by the customer. Then, you post the document or generate a warehouse release. At this point, two problematic situations could potentially arise. The first case is still relatively friendly: an error appears in the system, informing you that the stock quantity is insufficient. The second option is much worse: you waste the warehouse worker’s time for them to return with the same information – lack of stock to fulfill the order.
This way, you lose time that could have been spent enjoying a good coffee. The error doesn’t indicate how much stock is missing or how much is available, so you have to check everything manually. Something needs to be done about this. You then go to the inventory list to check the value in the Inventory column. The first item – the stock is sufficient. You check the second item… what was it again? And then you need to return to the sales document to check the order. Ultimately, it turns out that one screw was missing, and fifteen minutes are irretrievably lost.
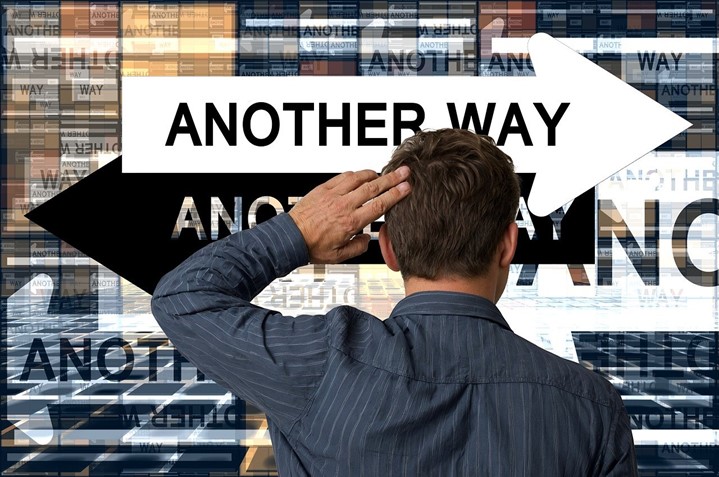
But it could have been different...
A column with information on the current stock level in the sales document would have sufficed. Then, it would immediately be visible that we want to sell 100 units of stock, but the stock level is only 99 units, which prevents the full order from being fulfilled. However, it’s just a column that you have to look at and analyze. It would be easier if, additionally, all lines with low stock levels were marked in yellow, and lines with critically low or zero stock were marked in red.
And what if we acted proactively and eliminated the risk of missing stock before it actually occurs? All it would take is to have one place where you can freely view all stock and filter it by a specific location.
It can be different!
Thanks to the Inventory Levels functionality, all of this is possible. In documents where insight into stock levels is crucial, we see a column showing the current stock quantity in the warehouse. Additionally, lines are color-coded based on the stock quantity at a given location, making it easier to quickly identify potential problems.
This allows for the immediate detection of potential issues in the document and saves the time you would spend manually checking stock levels. Additionally, we have provided a page within the functionality where all the company’s stock is visible.
This page makes it easy to determine which stock items are running low, why this is happening, and shows the current stock availability. The list can be filtered by selected locations and stock items, which significantly facilitates insight into where the stock is located and what is happening with it.
You can start using Inventory Levels today!
The functionality is available in our product – Advanced Inventory. The product is available immediately, and by ordering it now, you will receive a 20% discount. Just mention this article when talking to us.
If you’re interested in our solution or need help managing inventory levels, use the form below and contact us.
You can find Advanced Inventory on AppSource and on our website.