In a steel processing plant, where work continues day and night, one of the main challenges was managing the priorities of production orders. Steel, which must be precisely processed and delivered on time, requires perfectly organized production. Without a priority system, managing the process often turned chaotic. Every order was treated equally, with no distinction between standard orders and urgent requests from key clients.
Daily chaos
Every day, Tomasz, the production manager, tried to keep up with client demands. For operators, changes in plans meant disorganization. One day, Tomasz received a phone call from the plant’s largest client, urgently needing a batch of steel to complete a construction project.
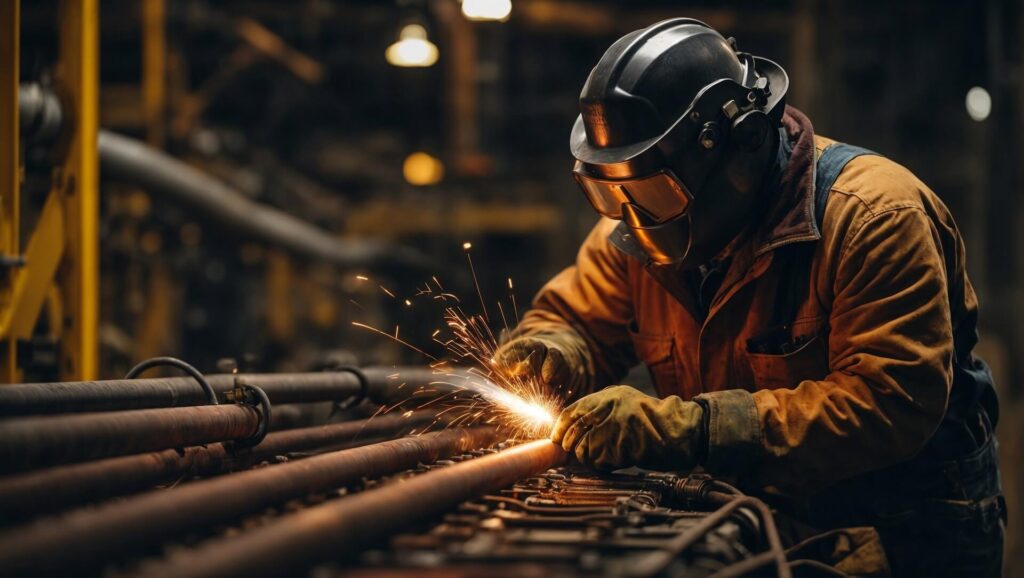
Unfortunately, no one on the production floor was aware of the urgent order. When Tomasz tried to convey the information, problems arose—one operator was already engaged in fulfilling another order, and others couldn’t easily abandon their current tasks. The lack of priorities led to frustration, as neither managers nor operators knew how to organize their work to meet client expectations.
Without the ability to visually highlight urgent orders, employees struggled to react quickly and efficiently to dynamic changes. As a result, some orders were delayed, leading to dissatisfied customers and financial losses for the plant. Tomasz knew he had to make a change. The solution was clear: a priority system was needed.
Introducing priorities – a new order
Thanks to the priority feature introduced in Business Central and the Nav24 Shop Floor Panel, the workflow in the plant started to change. Each order could now be assigned a priority, and any status changes were immediately visible to everyone.
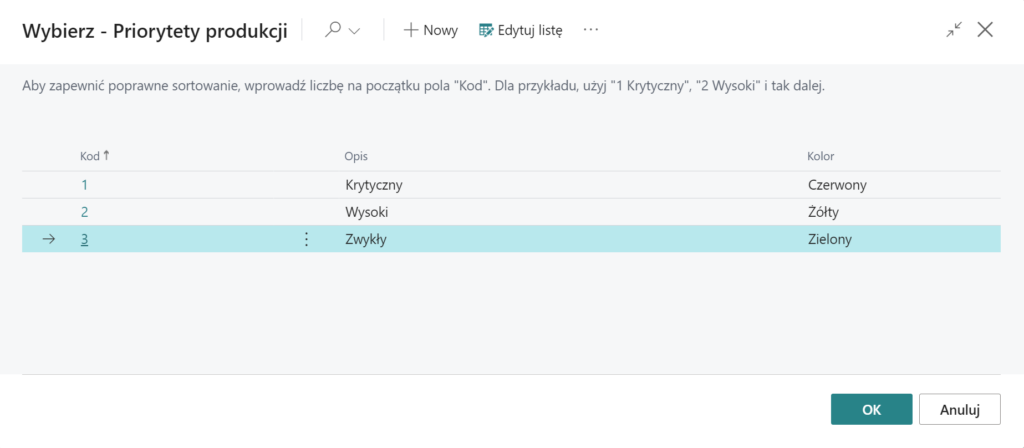
What’s more, priorities were color-coded on operator panels—high-priority orders were clearly marked with descriptions and a red color, while less urgent tasks were assigned corresponding colors configured in Dynamics 365 Business Central.
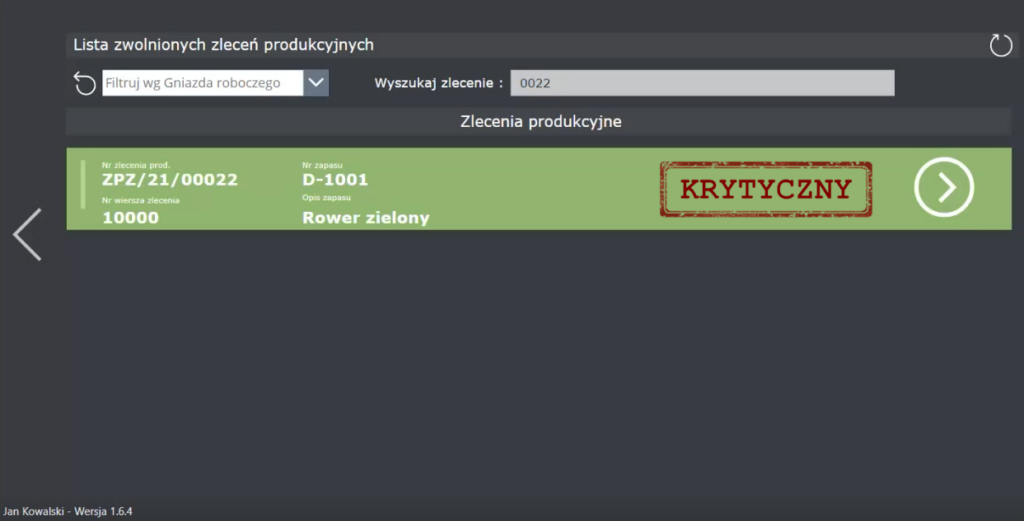
Shortly after implementing this solution, the plant received another urgent order. This time, it was enough to assign the highest priority to it in the system. On the operators’ production panels, the order immediately stood out in red. Without unnecessary questions, the operators knew they had to handle it first.
The impact of the new system
Thanks to the priority function, production started running smoothly without delays or stressful conversations. Operators had clarity on which tasks required their attention, and the manager could monitor in real-time whether critical orders were being completed on time.
Implementing priorities not only streamlined production but also provided the production team with a new level of comfort and organization in their work.
From then on, the company could quickly and flexibly respond to its clients’ needs, maintaining production flow even in the most challenging situations. Nav24 Shop Floor became a key tool in daily production management, giving the plant stability and a reputation as a reliable partner—regardless of the circumstances.
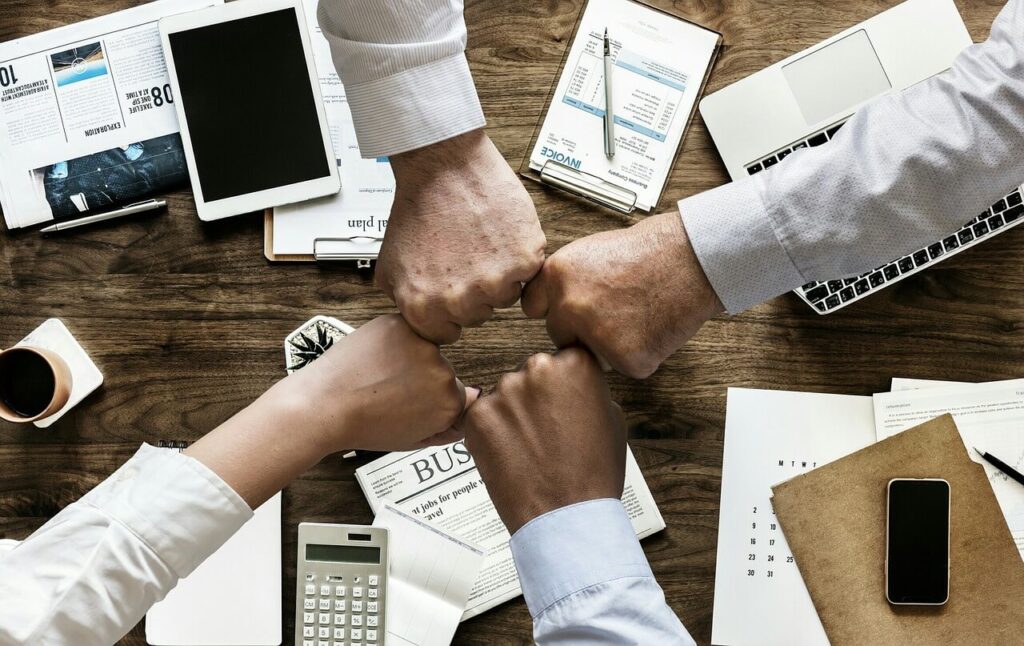
Want to learn how our solution can improve your production processes? Contact us and discover the full potential of this advanced tool!